In this exclusive interview, Graham shares invaluable perspectives on Versalift’s National Support and the pivotal role our van mounted access platforms play.
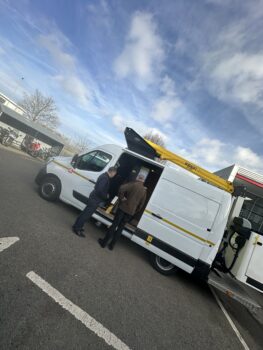
Head of Sales, Chris Wrenn pictured left, with Graham Papierowski, right, inspecting the Brand New Van Mounted Access Platform VTL-140-F on a Renault Master

Versalift United Kingdoms New Innovation – VTL-140-F Renault Master

VTL-140-F Van Mounted Access Platform on a Renault Master outside Versalift HQ.
GET READY TO UNCOVER THE SECRETS TO OUR COLLABORATIVE SUCCESS AND DISCOVER HOW INNOVATION AND PARTNERSHIP ARE DRIVING US FORWARD. LET’S DIVE INTO THE CONVERSATION!
Can you briefly describe your experience with Versalift and how long you’ve been using our van mounted access platforms?
“Overall experience with Versalift is positive and very good. I have been dealing with Versalift now coming up to eight years. I had no experience in the industry what-so-ever, Versalift went through their products with me, explained them in detail to our customers and my staff, so overall, perfect.”
What were the main factors that influenced your decision to choose Versalift for your Van Mounted access platform needs?
“Our main reason was down to customer acceptance, it’s what our customers ask for. They like the Transit van and they like the Versalift VTL platform. It does everything it says it is going to do, so that’s our main reason.”
On a scale of 1 to 10, how satisfied are you with the performance of your Versalift Van Mounted access platform?
“9.5”
Can you share a specific instance or project where Versalift’s equipment made a significant difference for your team?
“I haven’t got a specific, but within the fibre industry, which is where 80% of our business comes from at the moment, the Versalift platform will do more than the competitors. For instance, they’ve got extended reach, they’re easier, to a certain point, to operate and set up. And that’s where they’re mostly used and people love them.”
Would you recommend Versalift to others in your industry?
“100% I would recommend. Versalift are easy to deal with and are a good product. Nine times out of ten, if there is a major issue with the product, they rectify it. And their support and their backup in the field is second to none in my opinion. They’ve got their own engineers, and they’ve got a support network out there of subcontractors. So, if you really are in trouble, they get you out of it.”
How has Versalift contributed to the overall efficiency and productivity of your operations?
“Extremely difficult to answer to that question because, unfortunately, we don’t gauge productivity. All I know is we started the business with nothing eight and a half years ago, and now we’ve got over 100 vehicles, most of which are Versalift. The Versalift product is obviously doing something right.”
In your opinion, how does Versalift stand out from other brands in terms of quality and reliability?
“Over other brands, the Versalift product stands out because of the innovation of the VTL platform. The fact that it’s got the extended reach it can do what it says it can do, basically. I’ve never come across an incident where it won’t do what it says it’s going to do. Other manufacturers basically copy Versalift, in my opinion. They’re not as far as advanced as Versalift in the marketplace. Versalift were the first company to put the emergency control valves from the top of the platform to the back of the van, for instance. That makes a massive difference to a platform in any way, shape, or form. When you’re trying to get someone down that’s stuck, it’s easy to do it in the back of the van instead of having to climb on the roof to do it. To me, that was one of the biggest changes for the Versalift product.”
Could you elaborate on your Highway Hire’s commitment to safety and how Versalift’s equipment aligns with those safety goals?
“Yeah, 100 %. Safety is paramount for anything that’s lifting a person into the air and working at height. Versalift is constantly trying to evolve with different ideas of how they can save someone’s life if they’re stuck, for instance. They’ve got crush zones on the platform and in the basket. All the main cutouts/emergency stops, shut the entire vehicle down. Other manufacturers haven’t got the same set up. So overall, Versalift, again, extremely safe to operate because of the VTL.”
Have you noticed any specific safety features in Versalift’s equipment that you find particularly beneficial?
“A van mount is a completely different piece of equipment to operate. With all the sensors and all the safety features that Versalift have on their product, they’ve tried to take away the danger factor. For example, the operator won’t be able to turn that van over, because the platform won’t allow him to do so, it will stop working before then. It’s got the emergency stop buttons and it will shut the entire van down. But it also allows them to do their work that they need to do because it’s got the extended reach. I’ve personally used the platform on operating jobs, I’ve used the platform at home, and I’ve put it into situations where I’ve put it to its full reach, and it stopped me doing the operation so I couldn’t overload it. To me, that’s what it’s all about, to keep everybody safe but productive. They are very reliable products all round, and it is all about the support you offer afterwards which is key with any manufacturer.”
How has Versalift supported your team in terms of training and ongoing maintenance to ensure the longevity of your van mounted access platforms and the safety of your operators?
“Support-wise, like I mentioned earlier on, Versalift have a team of their own engineers, factory-trained. I’ve met the majority of these and worked with the majority of them on site. Their knowledge is second to none on their product, and it’s been great. They have a fantastic team of subcontractors that they’ve set up. Again, all trained on the product to keep your platform working, keeping it working in a safe practise. In addition, Versalift offer a very good LOLER inspection. And when it comes to oil filter changes, where others are not as extensive, for instance they don’t grease the vehicle correctly or the platform correctly, Versalift do it all. Whenever I’ve asked for training, I’ve got it. When I’ve asked for support, I’ve got it. I can’t ask for anymore.”
What features appeal to you in the Renault option with Versalift’s VTL boom?
“We do get asked for the Renault Master, and we do get asked for a Ford Transit, everybody knows Ford. Ford have been around for years and years. Renault Red Line is a relatively new player in the marketplace. Ever since the Renault Master came on the scene many years ago, supplied by the car manufacturer, it didn’t get a very good reputation for reliability. But now it’s being built by the truck manufacturer, which in turn is owned by Volvo. So you know that when you get your Renault Master, it’s been built in a truck factory, not a car factory. And it’s been built by Volvo. Everybody knows that a Volvo is an extremely reliable vehicle, and that’s what you’re getting when you have a Renault. The key feature with Renault is reliability. Support from a truck dealer, as opposed to a car dealer, is amazing, because they work 24 hours a day. If I had a choice, I would only buy Renault. But some of our customers want other products, because that’s what they’ve always had. And it’s all about introducing that new product, the Renault Master Red Line, into them.”
Through our conversation, we’ve delved into the integral role our van mounted access platforms play in driving productivity and safety in Graham’s operations.
Graham’s testimonial underscores the trust and satisfaction that our products instill in our customers. His commendation of Versalift’s dedication to quality, reliability, and safety echoes the sentiments of many others in the industry.
As we wrap up, we extend our gratitude to Graham for sharing his experiences and perspectives. His partnership exemplifies the collaborative spirit that propels us forward. Together, let’s continue to innovate, prioritise safety, and foster success in the Working At Height industry.